Product < Sandwich Panel < Operating Room Walls
Operating Room Walls
With the continuous improvement of hospital construction in China, the medical environment is receiving increasing attention from people. As the core field of hospitals, operating rooms have increasingly strict requirements for cleanliness and hygiene standards, so pollution control is becoming increasingly important in the construction of operating rooms. A clean operating room is an important means of controlling pollution. Reasonable and accurate selection of equipment and materials for the construction of clean operating rooms walls is a crucial step. At present, the main material selection for clean operating room walls is 1.0 mm-1.2 mm electrolytic steel plates, with a backing of 9-12 mm gypsum boards or calcium silicate boards supplemented by welding, polishing, and spraying of rails, keels system, hardware accessories, etc.
However, due to the complexity of the installation process mentioned above and the relatively high cost, Electrolytic steel plate handmade sandwich panel is a good alternative solution for operating room walls which can greatly reduce the construction difficulty and cost budget.

Comparison between traditional keel system and modular sandwich panel for operating room walls
1. traditional method of keel system
​
-
Welding and polishing on construction site, with keel system.
-
CAD design with strong arbitrariness, on-site construction, and quality determined by the level of construction personnel.
-
It is necessary to apply universal adhesive, cut gypsum board, cut square pipe, keel, angle iron on site, then weld, which results in high dust and harmful gases.
-
There is a lot of construction waste and noise, and the construction site covers a large area for material stacking, resulting in a messy site.
-
Welding and pasting gypsum boards on site are difficult for workers to construct and slow to install.
-
The traditional method is to hang electrolytic steel plates with a thickness of over 22mm on the square tube keel of 1.2 * 50 * 30 mm, backing by gypsum boards, total thickness is about 72mm, if double-sided wall, then total thickness is 94mm.
-
The traditional method involves making the keel, embedding the pipeline, making the base layer, and pasting the surface panel. The construction labor cost and materials cost are high.
-
It cannot be reused, it will be discarded after one time use.
2. Modular sandwich panel system ​
​
-
No welding on site, no keel and screw connection required.
-
Modular design, customized dimensions, no cutting on site, factory production
-
Double sided metal sheet, core insulation by aluminum honeycomb, rock wool, glass magnesium etc.,
-
Environmental-friendly and formaldehyde free
-
Fast installation speed, short construction period
-
The thickness of single sided and double-sided operating room walls is total 51 mm.
-
Reusable: the sandwich panel can be disassembled and reassembled for different projects.

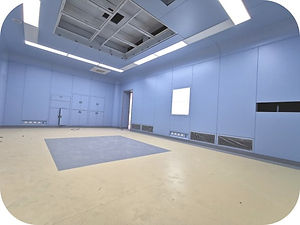
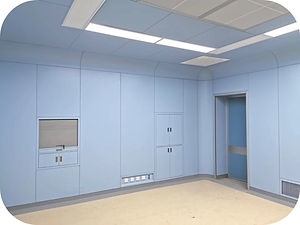
Operating room walls specification
-
panel thickness: 50 mm
-
panel width: 150 - 1220 mm
-
panel length: as project need, normally 2.4-3 m.
-
metal skin thickness: 1.0 / 1.2 mm
-
metal skin type: electrolytic steel plates
-
core insulation: rock wool, aluminum honeycomb etc.
-
color: blue, green, pink, white, ivory white etc.
-
connection way: by built-in alum.

Related Posts:
ASK A QUESTION
1. Are the operating room walls by machine made or handmade ?
Re: the operating room walls are a handmade type sandwich panel.
​
2. If the operating room walls width possible to be customized ?
Re: Sure, the operating room walls can be made according to your project need, you will no need to cut the panels on site.
​
3. Do you have the label to separate the operating room walls from other area ?
Re: Yes, we have a label system for different area of clean room as below, you will easily sort out the materials on site.

4. What is the packing method for the operating room walls ?
Re: It can be put into container by bulk, or packed into a wooden pallet or wooden case or according to your requirement.
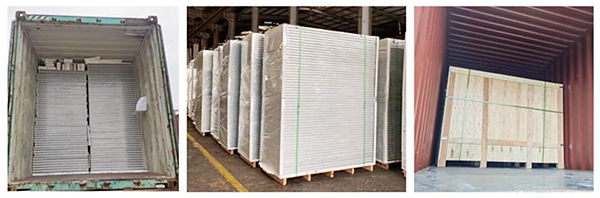